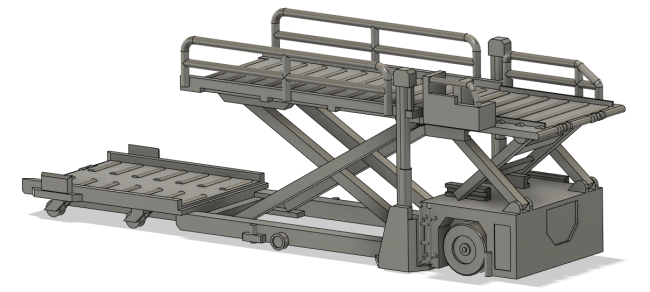
SK本舗ユーザーのリレーコラム#05「3Dプリンターで水洗いレジンを使用した際の反り対策と模型制作を考える」(今井誠)
1.ごあいさつ
皆さん、初めまして、やなかの技術士こと技術士(機械部門)の今井誠と申します。私はやなか技術士事務所で加工技術の困りごとや3Dプリンター、CADなどを使用したデジタルものづくりの技術コンサルタントをしております。今回、SK本舗様よりお声がけ頂き、3Dプリンターでのものづくりについてお話させていただきます。
私自身は3年ほど前に中古でFDM機を導入し、色々ものづくりを試していましたが導入後半年ほどでFDM機が壊れてしまい、修理もかなわずそのまま廃棄しました。その後、3Dプリンターの再導入も図るもなかなか縁がなく、やっと今年になってSonicminiに出会うことができました。現在、Sonicminiを使って色々な実験やものづくりを行っています。
2.3Dプリンターの導入について
FDM機が壊れた後、検討していたのは同じFDM機であるZortrax社のM200、その後株式会社久宝金属製作所様のQholiaの導入を検討しました。しかしながら、なかなか再導入のご縁がなく、そうこうしているうちに高嶺の花である光造形機の低価格ラッシュが始まりました。
私事ですが今年の4月に勤めていた勤務先を退職して技術士として独立して技術士事務所を開業する際、せっかく新しいことを始めるのだから技術士でやってる人が少ない技術分野を開拓してみようと考え、3Dプリンターを導入することにしました。その際、どうせなら低価格化が著しく、今後主流になるだろう光造形方式の3Dプリンターにすることに決めました。
光造形方式の3Dプリンターの導入にあたって、SLA方式、DLP方式及びLCD方式の違いを調べ、私の目的に合う機種を選択しました。私の場合、まずは様々な造形実験を行って3Dプリンターの技術情報を得ることが目的でした。その中で目を引いたのは、モノクロLCD機でした。LCD機は一度に露光領域を露光するのでSLA方式よりも造形速度が速く、さらにモノクロLCDはLEDのフィルターとなるLCDにカラーフィルターがないため、カラーLCD機に比べて単純に露光する光の強度が3倍になります。そのため、モノクロLCDは光造形方式の3Dプリンターの中でも造形速度が最も速くなります。造形速度が速くなれば、その分生産性が上がることから製造業でも導入を考える企業も出てくると考えました。このため、モノクロLCD機の造形条件や運用実績等の技術情報を得ることが仕事に対する費用効果が高く、導入機種をモノクロLCD機としました。
丁度、この時期に発売されていたのがSonicminiでした。ここでご縁があったのでしょう。タイミングよく、SK本舗様がSonicminiのセールを開始したので、迷わず購入しました。Sonicminiは筐体が非常に小型なので、仕事机の横に配置することができます。このため、パソコン等を使用した設計業務や原稿執筆等の傍ら、3Dプリントの状況確認や造形終了後の洗浄作業等にすぐに掛かることができ、時間を有効に活用することができます。
3.水洗いレジンについて
次に光造形の材料についてお話しします。光造形に使用されるのは光硬化性樹脂と呼ばれる液体の樹脂材料(以下、レジンという)というものです。レジンは紫外線(UV光)が照射されると光重合反応という化学反応を起こして固まります。光造形法は、この性質を利用して3次元造形物を造形するわけです。
レジンは、基本的にはUVレジンと呼ばれるものが主流です。このUVレジンは造形後にアルコールで洗浄する必要があります。このため、光造形機を運用していく上でそれなりの量のアルコールを使用します。運用コストを下げるためには、アルコールの使用量を減らすか、エタノールより安いIPAを使用することになります。
私が造形材料を選択する上で、このIPAが最大の懸念材料でした。私は、製造業で加工関連の仕事をしていましたので、有機溶剤を使用する際の危険性等を熟知しています。例えば、工場などのドラフトチャンバー等の換気設備が完備されている環境、加えて防毒マスクを着用した状態での運用については安心できます。しかし、事務所を自宅で開業する上で、仕事場が家族の生活スペースと隣接してしまいます。このため、IPAを自宅で運用することにはためらいがありました。また、個人がIPAを廃棄することについてもハードルが高いことがわかっていました。尚、皆さんも決して使用したIPAを下水に流さないでください。法律違反です。
そんな状況で、以前SK本舗様が開催された3Dプリンターのファンミーティングに参加した際に知ったのが水洗いレジンでした。水洗いレジンの利点は、造形後の洗浄に水道水を使用することです。つまり、IPAを使用しないで済むことでした。家族が生活する環境と隣接する場所で3Dプリンターを運用せざるを得ない私にとっては、一番大きなメリットでした。このため、3Dプリンターの運用開始から水洗いレジンをメインに造形を行っています。尚、比較実験のために少量のUVレジン、キャスタブルレジンを使用していますが、洗浄には健康リスクの低いエタノールを使用しています。
4.反り対策について
水洗いレジンを使用していく上で、気になったのがUVレジンよりも反り量が大きいということでした。造形直後から乾燥に伴って2、3日経過しても変形(反り)が続いてしまう現象に直面しました。
特に板状部材で反りが顕著でした。上の写真のものはプラットフォームに対して厚み方向がZ軸方向(つまり造形角度0度 水平姿勢)となるように出力後、水で洗浄後、日陰で二日ほど乾燥させたものです。初期のころは、剥離力等を考慮せず造形していたため、造形物の中央部に対して両端がZ軸方向に反り易い傾向にありました。
そこで、様々な造形姿勢での出力実験を繰り返しました。実験により長尺方向を80度~90度方向に配置することで反りを大幅に低減することがわかりました。加えて、短尺方向もプラットフォーム面に対して5度から15度程度傾けることで板状部材でもかなり反りを抑えた造形をすることがわかりました。
下の写真の板状造形物は、プラットフォームに対して長尺を85度、短尺を10度傾けた姿勢で出力しています。
また、出力後の反りについても、下の写真のように反りが抑制されていることがわかります。
いくつか条件を振ってみて実験した傾向として板状部材など大きな面を有する部材は、プラットフォームに対して造形物の面を正対させないことが重要なファクターであることがわかってきています。
次に、水洗いレジンで造形後の経時変化(変形)が少ない後処理について、私の経験を述べます。少し専門的な話になりますがお付き合いください。
光硬化性樹脂(レジン)は光重合という化学反応で硬化することは先に述べました。実はレジンには樹脂材料の観点からアクリル樹脂系の材料とエポキシ樹脂系の材料の2つがあります。実は、この2つの材料では光重合の反応様式が異なります。
アクリル系樹脂は、光ラジカル反応というもので反応速度が速く、光の照射が停止すると反応自体も停止します。しかし、光ラジカル反応は反応率が約70%程度であるので、残った反応基が二次硬化を行う際の紫外線の露光でも完全消費され難く、経時で徐々に反応します。
一方でエポキシ系樹脂は、光カチオン反応というもので反応速度が遅く、一旦反応が始まると光の照射が停止しても反応基がなくなるまで硬化反応が進みます。このため、エポキシ系樹脂は硬化反応が遅いながらも完全硬化するので、経時変化が起きにくい特徴があります。
現在市販されているレジン材料の多くは、このアクリル系樹脂にエポキシ系樹脂を混ぜた材料、光ラジカル反応と光カチオン反応のハイブリット樹脂です。アクリル系樹脂を含むため、造形後のレジンの二次硬化は必須になります。そして、二次硬化後もわずかながら経時変化が生じます。
これらを踏まえると、UV光を照射して二次硬化させることが重要です。多くの3Dプリンターを使用している人はUVランプを使用して短時間で二次硬化させている人も多いと思います。ここで問題になるのは、二次硬化の際、光重合反応で熱が発生するということです。もちろん反応基そのものの数は少ないので高熱になるような発熱まではいきません。しかしながら、硬化したレジンの中にはかなりの量の水分が含まれています。この水分が曲者です。硬化したレジンの中で水分が二次硬化時の熱で膨張するからです。そして、冷却されると今度は膨張から一転収縮に移ります。これらの体積変化が極短時間に生じると内部に応力が生じたり、クラックが発生したりします。その結果、経時変化とともにレジンのひび割れや損傷の結果になります。下に示す写真は急激に加熱した場合にレジンがどのように変化するかを実験したものです。
試しに二次硬化前のレジンを電子レンジで10秒ほど加熱したものです。電子レンジにより急激に加熱された水分が膨張してクラックが生じてしまいました。
したがって二次硬化の前にできる限り、レジン内の水分を減らすことが重要です。私の場合、出力後半日から1日程度送風機で送風して常温で乾燥させています。つまり、温度変化を極力抑えた状態で水分を減らし、その後二次硬化を行っています。この方法を始めてから5か月程度経過したレジンでもひび割れ等は発生していません。
5.模型製作について
(1)治具製作について
ある程度、造形条件がわかってきたところで、自分の趣味の模型製作に3Dプリンターを活かしたものづくりの模索を始めました。最初にTwitterで知って以来、自分で作って使用していた“つまようじヤスリ”を簡単に大量に作れないか考えました。治具設計は本職だったので、いくつかテスト造形した後、自分にとって使い勝手のよい治具を作りました。写真の治具をTwitterにツイートしたところ、何人かの方が興味を持ってくれたので試しに販売したところ、思った以上に売れました。正直、売れるとは思っていなかったのでうれしい誤算でした。
(2)地上支援車両(GSE)について
元々、学生の頃から飛行機好きで飛行機に乗るのが好きでした。学生のときに行ったアメリカの空港で初めてダイキャスト製の旅客機モデルを見て購入しました。その後、ダイキャスト製の旅客機の購入熱は定期的に熱が上がったり下がったりとしていますが、コツコツと集めていました。
おそらく、飛行機模型を集めている人の中には、飛行機が好きなだけでなく空港という場所が好きな人もいらっしゃるはずです。実際、私も非日常感を味わえる空港が好きです。集めた飛行機模型で写真のように手軽に空港の情景を再現したりもしています。コロナの自粛中、旅行にも行けないので、動画サイト等で空港を映した動画を見ていました。その際に、旅客機の周囲を走り回る地上支援車両(GSE)を見ていて欲しいなと思いました。
しかし、旅客機のダイキャストモデルは色々な機種や航空会社のものがモデル化されているのに対して地上支援車両については海外の会社や国内の食玩メーカーのおまけ程度でその種類も少なく、販売数自体も十分でないため売っていても高価な場合がほとんどです。さらに海外メーカーのものは、ヨーロッパの地上支援車両をモデルにしており、日本国内のものと形も違います。そのため、国内航空会社の周りに配置すると違和感が生じます。この違和感が日に日に大きくなってきて、日本の空港で見られる情景を再現したいと思いました。そして、せっかく精度の高い3Dプリンターがあるのだから、海外のメーカーの地上支援車両よりも精度の高いものを作ろうと思いました。
(3)地上支援車両(GSE)の製作について
最初に作ろうと思ったのは、飛行機に乗った際によく窓から見ていたハイリフトローダーです。食玩等のおまけでも立体化されていなかったので、これを作って自分の空港を賑やかにしようと考えました。
まずは、資料集めです。ネット等で画像や映像、さらには製造メーカーのシンフォニアテクノロジーさんのHPから3面図や諸元を入手します。これらを基にざっくりとした3Dモデルを作成しました。このモデルを基にして詳細なディテールアップと、フロントデッキを上昇させたモデル、フロントデッキ及びリアデッキを上昇させたモデルを作成しました。
これらのデーターを完成させたら、まずはテスト出力です。3Dプリンターは高精度で出力が可能な機械ですが、それでも出力の限界があります。ですから、どんなに3DCAD上で高精細なデーターを作っても出力できなければ意味がありません。
上の写真は、一番最初にハイリフトローダーを出力した状態です。写真を見てお気づきだと思いますがフロントデッキ、リアデッキの手すりの柵がないですね。
こちらの写真を見てもらえればわかりますが、もじゃもじゃとしたものが見えます。UV光が露光されて樹脂が硬化するところまではきちんといっていますが、柵の部分に強度がないため、FEPフィルムから剥離する際に壊れてしまっています。
ちなみに、この時の柵の出力径は0.1mmでした。その後、柵の径を見直して何度か出力テストを繰り返しました。
この写真は柵の径が0.25mmで出力したものです。
出力はされたものの、全く強度がなく、二次硬化させるとすぐに破損してしまいました。
下の写真は柵の径を0.3mmで出力したものです。このサイズまで来るとやっと安定して出力されてきています。また、強度的にもなんとか模型として取り扱いに注意すれば、手に取っただけで破損してしまうということはなくなりました。
したがって、どんなに3DCADのデーターが高精度であっても模型としてみた場合、出力可能なサイズには限界があるということです。そのため、実在の機械を忠実にスケールダウンしただけでは、模型として成り立ちません。ある程度のデフォルメが必要になってきます。その辺の匙加減が非常に難しいと考えます。
次に直面した問題は、造形姿勢です。単純に直方体のモデルと考えた場合、全ての面の精度を出そうとすると、先に述べたように一点を中心にプラットフォームに対して面を傾ければある程度の精度は得られます。
しかしながら、模型の場合、形状が複雑すぎて全ての面をプラットフォームに対して傾けることが難しく、さらに形状によってはサポートが絶対に必要な部分が出てきます。
上の写真は、Cituboxでハイリフトローダーのモデルデーターにオートサポートを付加した状態の図です。見ればわかるように、細かなディテールを潰すようにサポートが付いてしまっています。この段階でハイリフトローダーの出力物を造形する上でオートサポートは使えないと判断しました。そこで、3DCADを使ってサポートも設計していくことにしました。
この写真は初期のサポートと造形姿勢です。初期はオートサポートの位置を参考にしつつ、必要最低限のサポート数になるように試行錯誤していました。左の写真のように重量のある車両前部がプラットフォーム側に位置することで出力時の姿勢の安定や剥離時の出力物の揺れ等を減らそうと意図していました。
しかしながら、出力してみると丸の部分が段差になっているのですが、ここにレジンが溜まり、ディテールがはっきりとでないことがわかりました。しかも車両の前方部分ですから目につきやすいところです。したがって、この部分の造形をはっきりさせるために造形姿勢を思い切って逆に変えました。
車両前方側をFEPフィルム側に配置したことで車両前方部分に液だまりができることがなくなり、ディテールがしっかりと出力されるようになりました。
しかしながら、1つ解決すると次の問題が出てきます。重量のある車両前方部分をプラットフォームに対して下方側に配置したので、車両前方側を出力する際に剥離力に耐えられず、印刷ミス(SKショーコちゃんの言うところの印刷死)が増えました。特に車輪をサポートする部分で接続がはがれ、脱落する例が増えました。しかし、車輪部分のサポートを厚くすると切り離し時に車輪の形状が崩れるおそれもあるため、厚くすることができません。そこで、底面に円柱状のサポートを追加しました。接続部分も円柱に近い形にすることで接続面積を稼ぎつつ、レジンが流れやすく設計しています。
これらのサポートの見直し、追加により一部、印刷ミスはあるものの、安定して造形ができるようになりました。
ちなみに、ここまで到達するための試行錯誤についてかなり省略しています。下の写真は、実際にテスト出力した出力物の一部です。実際は、この4倍ほどを出力して印刷精度等を確認して、修正、再出力、確認といった流れを行っています。
ここで、痛感したのはSonicminiの印刷速度の速さです。このモデルであれば約5時間程度で出力できます。一日に3回の試行錯誤が出来るわけです。これは開発者にとって、開発速度の大幅なスピードアップにつながります。通常、開発者は試作品を作って評価して再試作までの流れを1週間単位で行っています。しかし、Sonicminiであれば、1週間かかっていたものを半日程度まで短縮できるのは凄いと考えます。製造業の開発工程で光造形機、特にモノクロLCD機を導入する価値はあると考えます。
(4)地上支援車両(GSE)の販売について
話が前後しますが、ハイリフトローダーの試作品をTwitterでアップしていたころ、1通のメールが届きました。開いてみると英文でした。最初はいたずらメールかと思いましたが、翻訳してみると私のハイリフトローダーの出来を評価する内容でした。そして、出力物が欲しいとのことでした。何回かやり取りしているうちに販売してくれないかとの打診があり、ECサービスに興味もあったのでBooth(https://yanakadigifac.booth.pm/)にてサイトを作成し、販売することにしました。実際に販売してみるとTwitterを見て購入してくれた方が多く、精度等にも高い評価を頂いたことが開発者としては非常に嬉しかったです。最初に1/500スケールで販売していましたが、すぐに1/400スケールでも販売してほしいとの声が届くようになりました。
(5)スケールサイズ(1/500スケール、1/400スケール)の違いにおける設計の注意点
3DCADのいいところはデーターを簡単に拡大縮小できるところです。データーは1/500スケールサイズを念頭に設計してあります。単純に1.25倍すれば1/400スケールサイズになります。実際に1.25倍で出力してみたところ、太くなってほしくないところまで太くなってしまい、精密感が薄れた感じがします。結局、元データーを1.25倍に拡大した後、精度が欲しいところは1か所ずつ寸法を小さくするという作業を行いましたが、納得のいく出力精度になったと考えます。
3DCADのようにデジタルデーターはスケールサイズを変更することが容易にできますが、全体のバランスを各スケールサイズで見直すことが必須になります。実は、模型全体の出来としては1/400スケールの方が上です。何故か?それは模型の各部寸法のバランスが実車の寸法のバランスに近づいたためです。さらに、1/500スケールでは小さすぎて安定して出力できない部分もサイズアップに伴って出力できるようになったからです。例えば、1/400スケールでは、1/500スケールで出力しきれなかったリフト機構のチェーンブロック(赤丸部分)まで出力しています。
第1弾のハイリフトローダーでは、スケールサイズの異なる2つのサイズでの販売、さらには元々販売を考えていなかったこともあり、開発手法としては泥縄式でした。そこで、第2弾のカーゴトラクター&ドーリーセットでは、当初から2つのスケールサイズを意識して、高精度のオリジナルデータを作成し、そのデーターを基に1/500、1/400スケールのデーターを作成してテスト出力、微調整を繰り返して完成させました。左の写真では1/500スケールのトラクターのウインカーは出力できるように大きく設計してあり、1/400スケールではもとのデーターのままで出力が可能なのでそのままにしてあります。両スケールを見比べると微妙に設計を変えていることがわかります。
6.おわりに
Sonicminiと出会ったことで自分の技術者としての仕事の幅が広がったと思います。一年前にはまさか、自分が3Dプリンターでミニチュア模型を製造・販売しているとは思いませんでした。また、ブログ等を介して3Dプリンターの初心者向けの記事のアクセス数の多さにも驚いています。今後も「やなかの技術士」としてTwitterを中心に3Dプリンターや技術的なこと、初心者向けの記事をツイートしていきたいと思います。
地上支援車両(GSE)については、今後更にラインナップを増やしていきたいと考えています。ご興味のある方はTwitter等で情報発信していますのでDM頂ければ幸いです。
著者名:今井 誠
2008年に技術士(機械部門)を取得し、2020年4月にやなか技術士事務所を開業。放電加工やAM(付加製造)を中心に、加工技術の「困りごと」に対応しています。Twitterではやなかの技術士を名乗って日々、放電加工や3Dプリンティング技術、デジタルものづくりについてつぶやいています。
URL:https://www.yanaka-proengineer.com
Twitter:@HPcfc4aTx6uYPAp
GSE等の販売サイト
やなかデジタルファクトリー:https://yanakadigifac.booth.pm/
SK本舗ユーザーのリレーコラム
#01「Phrozen Shuffleで模型鉄」(ナガイケンタ)
#04「SLAプリンタの剥離抵抗と、より高精細な造形をするためのヒント」(IKE)
#05「3Dプリンターで水洗いレジンを使用した際の反り対策と模型制作を考える」(今井誠)